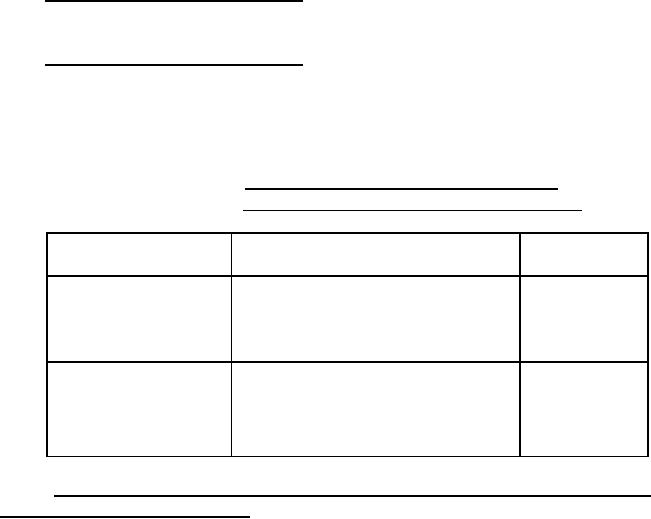
MIL-A-62463B(AT)
b. Alternately apply pressure to ports 2 and 17 for type I actuator or to ports 2 and 7 for
type II actuator, and cycle shaft 15 times in each direction of rotation. Apply
3200 ± 200 psi (22,064 ± 1,380 kPa) for 5 seconds at each end of cycle (at full rotation).
c. Apply 3200 ± 200 psi (22,064 ± 1,380 kPa) to port 2, with the shaft secured in mid
position. Hold 3200 ± 200 psi (22,064 ± 1,380 kPa) and measure leakage from port 7b
(see 4.3.2).
4.6.8 Combined leakage, type II actuator. To determine conformance to item 3 of table III,
calculate the total of the two leakage rates measured in 4.6.7.1 and 4.6.7.2.
4.6.9 Port 11 wheel valve O-ring leakage. To determine conformance to item 3a of table I:
a. Apply 3200 ± 200 (22,064 ± 1,380 kPa) to port 11 and hold this pressure.
b. Measure leakage at ports 7A and 7B (see 4.3.2).
TABLE VII. Wingshaft Rotation Positions for Vane Seal
Leakage Tests and for Breakout PressureTests.
Shaft Position (CCW Rotation
Port Appplied
Angle from Full CW)
with Pressure
Type I Actuators
5°±5°
Port 2 side B
corner
36 ° ± 5 °
Port 2 side B
36 ° ± 5 °
Port 17 side B
67 ° ± 5 °
Port 17 side B
Port 2 side A
Type II Actuators
5°±5°
Port 2 side A
(Intermediate)
36 ° ± 5 °
Port 7 side A
36 ° ± 5 °
Port 7 side A
67 ° ± 5 °
4.6.10 4-7A Wheel valve leakage, 1-2 wheel valve leakage, shock check valve leakage and
leveling "drain" valve stem leakage. To determine conformance to items 3b, 3c, 4, and 6b of table
I:
a. Apply 3200 ± 200 psi (22,064 ± 1,380 kPa) to port 11 and hold this pressure.
b. Plug port 3.
c. Apply low pressure to port 2 and rotate shaft to full clockwise position.
d. Remove plug from port 3.
15
For Parts Inquires call Parts Hangar, Inc (727) 493-0744
© Copyright 2015 Integrated Publishing, Inc.
A Service Disabled Veteran Owned Small Business