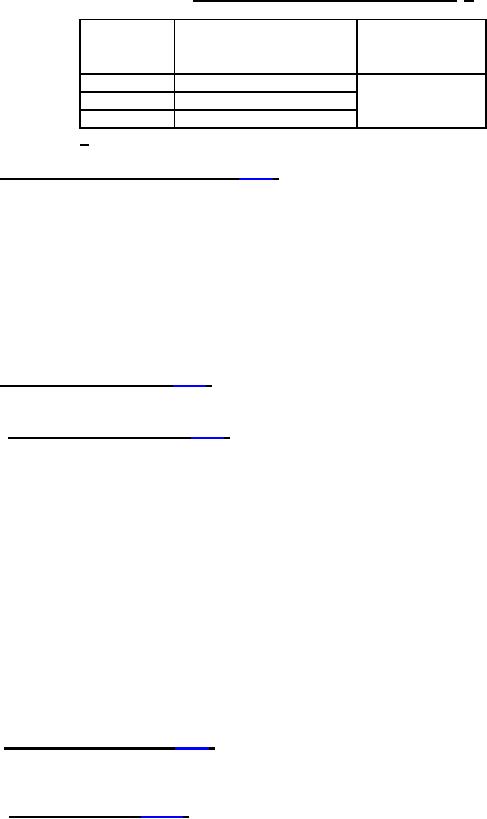
MIL-DTL-13719G
TABLE IX. Slack required for fatigue life (whip) test. 1/
Free length
Hose ID
Slack required
between fittings
inch (mm)
±.015 inch (±0.38 mm)
inch (mm)
.125 (3.18)
1.750 (44.55)
.188 (4.78)
1.000 (25.40)
14 (355.6)
.250 (6.35)
1.000 (25.40)
1/ Metric equivalents are given for information only.
assemblies shall be tested as in accordance with SAE J1401 with the following exceptions:
a. Hose assemblies shall be conditioned for 72 hours at a temperature of -65°F ±4°F (-54°C ±2 °C).
b. At the end of condition and while still at the specified temperature, the sample shall be bent, within
10 seconds, through 180° from the centerline over a mandrel with a diameter equal to 10 times the
nominal outside diameter (OD) of the hose. While still at the specified temperature, the sample
shall then be bent through 360° in the opposite direction over the same mandrel within the next 10
seconds.
c. After completion of the bending at the specified temperature, the sample shall be subjected to the
proof pressure test (see 4.5.4).
4.5.9 Tensile strength test (see 3.5.7). To determine conformance to 3.5.7, hose assemblies shall be
tested in accordance with SAE J1401.
4.5.10 Ozone resistance test (see 3.5.8). To determine conformance to 3.5.8, hose shall be tested in
accordance with SAE J1401. The following details shall apply:
a. The exposure chamber shall maintain a mixture of air and ozone in the proportion of 50 ±5
parts of ozone per 100 million parts of air by volume, and capable of maintaining an air
temperature of 100°F ±2°F (38°C ±1°C).
b. The test shall be conducted in an ambient temperature of 100°F ±5°F (38°C ±3°C).
c The sample shall be bent around a mandrel, the diameter of which shall be 7 times the OD of
the hose being tested, and bound with twine or tape at the point where the ends of the hose
cross one another. If collapse of the hose occurs, provisions shall be made to support the
hose internally.
d The sample shall be conditioned 45 minutes in air at room temperature.
e. The sample, while still on the mandrel, shall be placed into the chamber and exposed to the
mixture of ozone and air for a period of 168 hours.
f. At the end of the 168-hour period, the hose cover shall be examined under 9-power
magnification, ignoring the areas immediately adjacent to or within the area of the sample
where taped or tied.
be tested as in accordance with ASTM D471, except the aging shall be for 70 hours at a temperature of
212°F±5°F (100°C±3 °C). The immersion fluid shall conform to MIL-PRF-46176.
subjected to a 96-hour salt spray in accordance with ASTM B117, and subsequently proof pressure
tested in accordance with 4.5.4.
12
For Parts Inquires call Parts Hangar, Inc (727) 493-0744
© Copyright 2015 Integrated Publishing, Inc.
A Service Disabled Veteran Owned Small Business