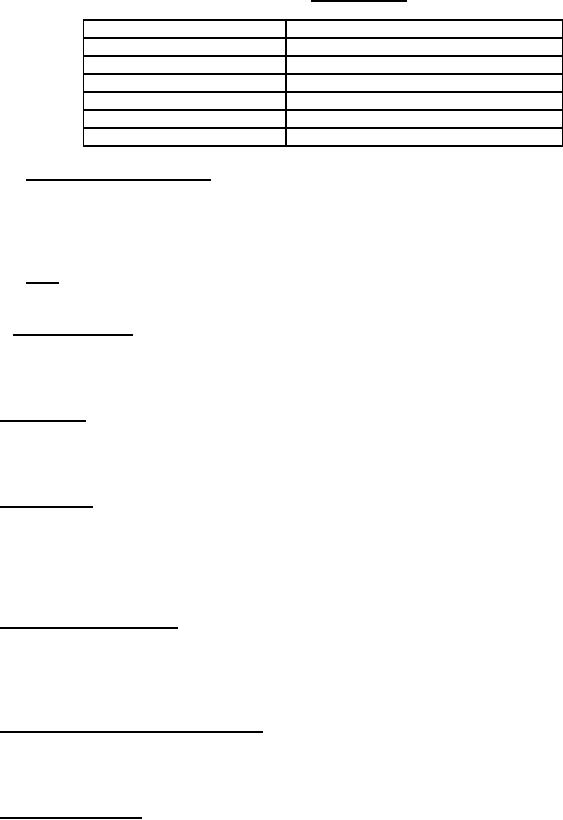
MIL-DTL-14055G
TABLE III. Loss in weight.
Metal
Loss in Weight mg/sq cm, Max.
Tinned iron
0.2
Steel
0.2
Aluminum alloy
0.1
Cast iron
0.2
Brass
0.4
Copper
0.4
3.4.6.2 Disintegration of rubber cup. The rubber cup exposed to the brake fluid-water mixture shall show
no sloughing, tackiness, blisters, nor any other form of disintegration. (Sloughing is indicated by the
presence of carbon black on the surface of the rubber cup.) The base diameter of the cup shall not
increase more than 0.050 inch (1.3 mm). The hardness of the rubber shall not decrease more than 15
points. (see 4.7.7.3)
3.4.6.3 Fluid. Following the corrosiveness test, the test fluid shall show no jelling or crystalline deposit,
and shall contain not more than 0.05 percent (by volume) precipitated matter. (see 4.7.7.3)
3.4.7 Storage corrosion. When cylinder cups are tested as specified in 4.7.8 there shall be no evidence
of corrosion adhering to or penetrating the wall of the test cylinder bore which was in contact with the test
cup. Slight discoloration (staining) or corrosion away from the contact surface of the test cups shall not
be cause for rejection.
3.5 Identification. The part or identification number (PIN) shall be marked on the package and shall
include the PIN, the manufacturer's name or CAGE code, and date code. The identification mark of the
manufacturer and other marking as specified on applicable drawings (see 6.2) shall be molded into each
cylinder cup.
3.6 Workmanship. Wheel cylinder cups, master cylinder primary cups, and master cylinder secondary
cups shall be processed in such a manner as to be uniform in quality and shall be free from burrs,
crazing, cracks, voids, pimples, chips, blisters, pinholes, protuberances, embedded foreign matter and
other physical defects that will adversely affect life, serviceability, or appearance.
4. VERIFICATION
4.1 Classification of inspection. The inspection requirements specified herein are classified as follows:
a. Qualification inspection (see 4.4).
b. Conformance inspection (see 4.5).
4.2 Test equipment and inspection facilities. Test and measuring equipment and inspection facilities of
sufficient accuracy, quality and quantity to permit performance of the required inspection shall be used.
The establishment and the maintenance of a calibration system to control the accuracy of all test and
measuring equipment shall be in accordance with ISO 17025 and NCSL Z540.3, as applicable.
4.3 Inspection conditions. Unless otherwise specified, all testing shall be conducted at atmospheric
pressure within the range of 28 to 31 inches of mercury (71.1 to 78.4 centimeters of mercury), a
temperature between 60°F and 100°F (15.6°C to 37.8°C), and a relative humidity of not more than 90%.
Tolerances of the test conditions shall be as follows:
a. Temperature: +10°F, -5°F (+5.55°C, -2.8°C)
b. Pressure (gauge): ±5%
5
For Parts Inquires call Parts Hangar, Inc (727) 493-0744
© Copyright 2015 Integrated Publishing, Inc.
A Service Disabled Veteran Owned Small Business